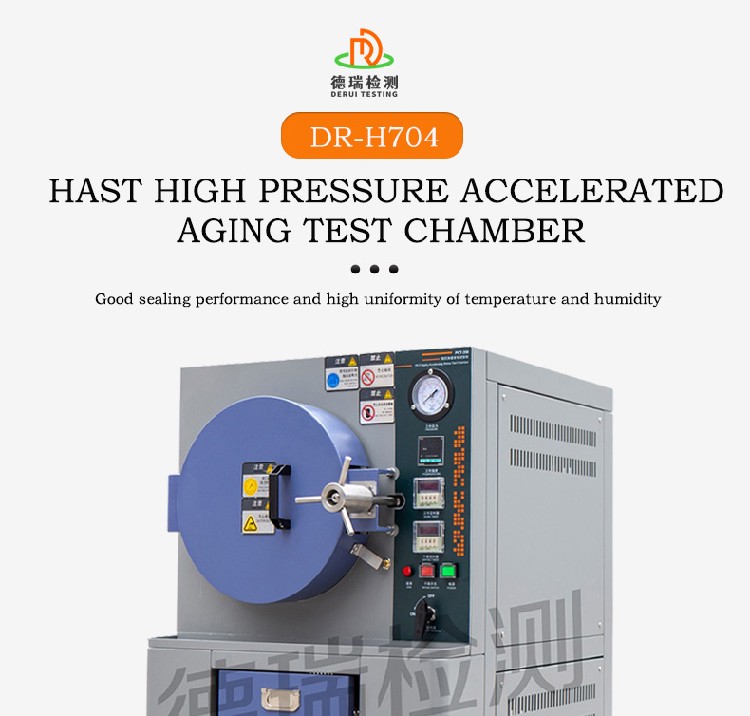
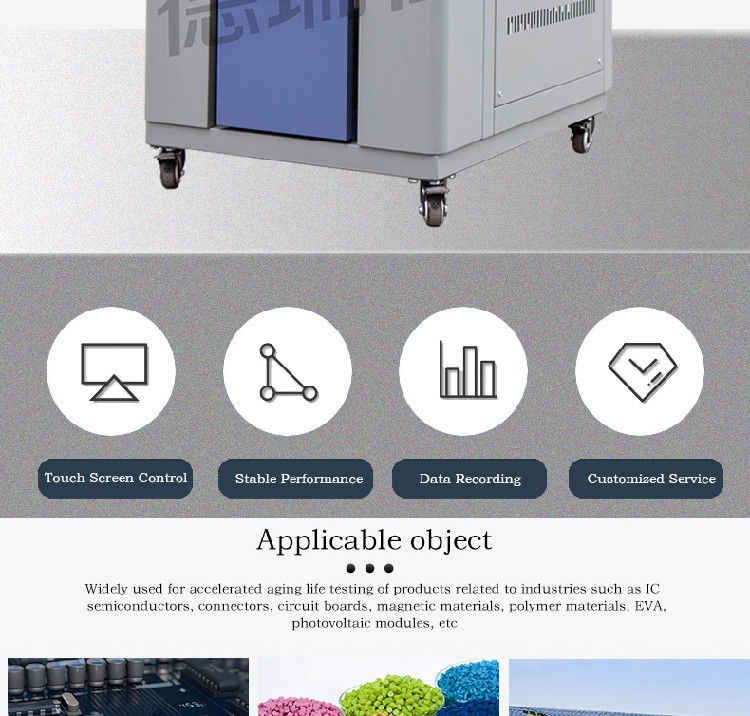
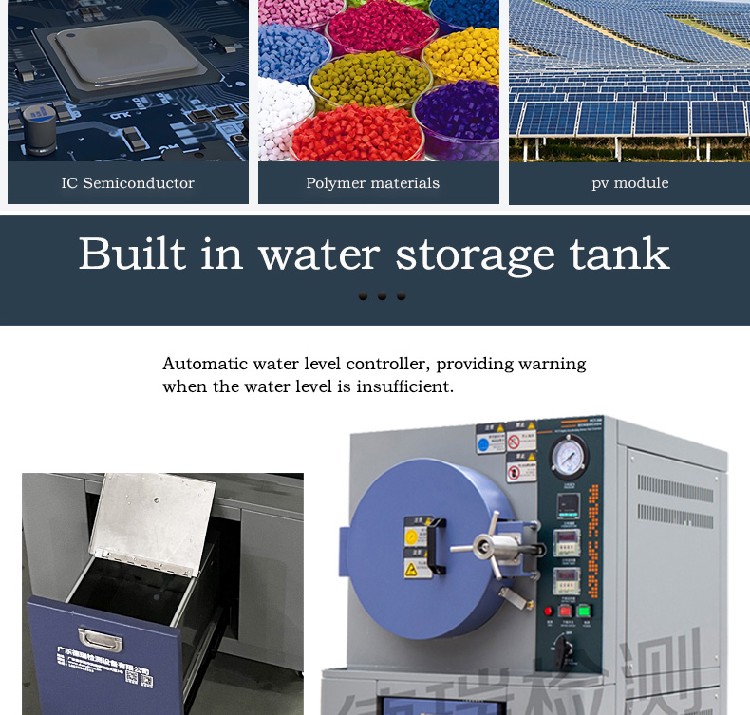
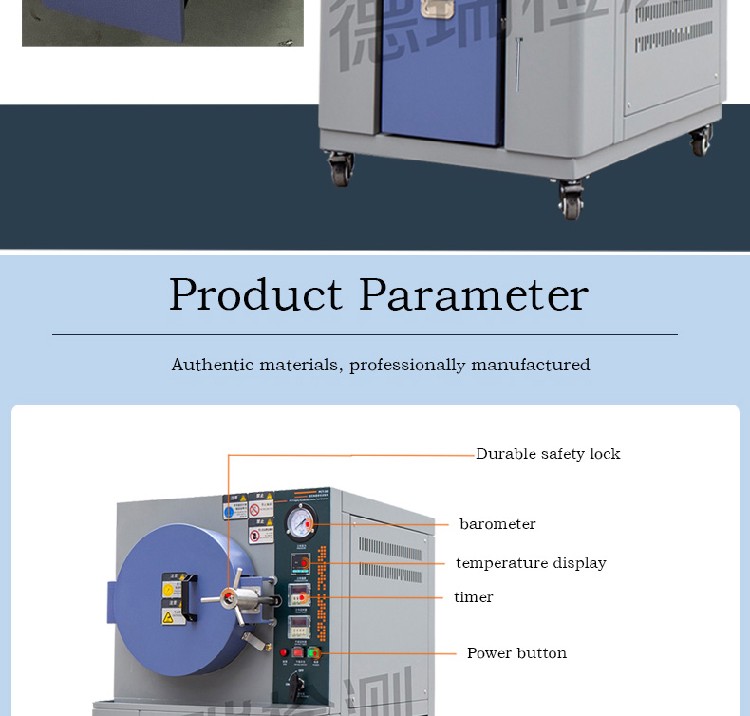
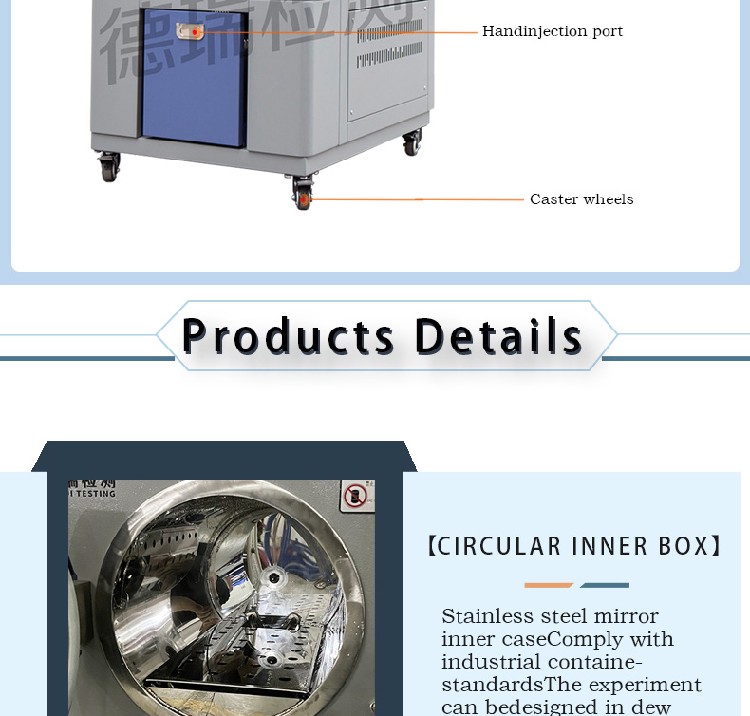
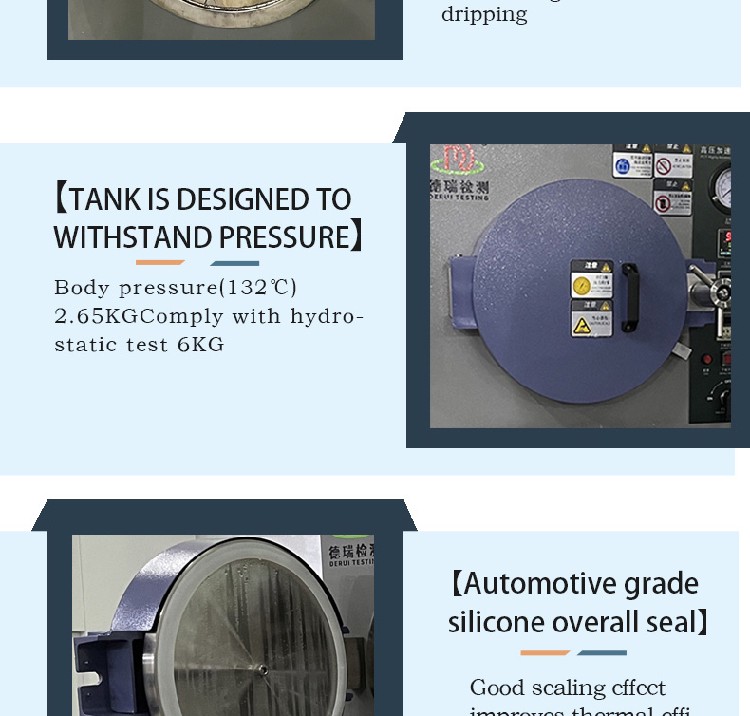
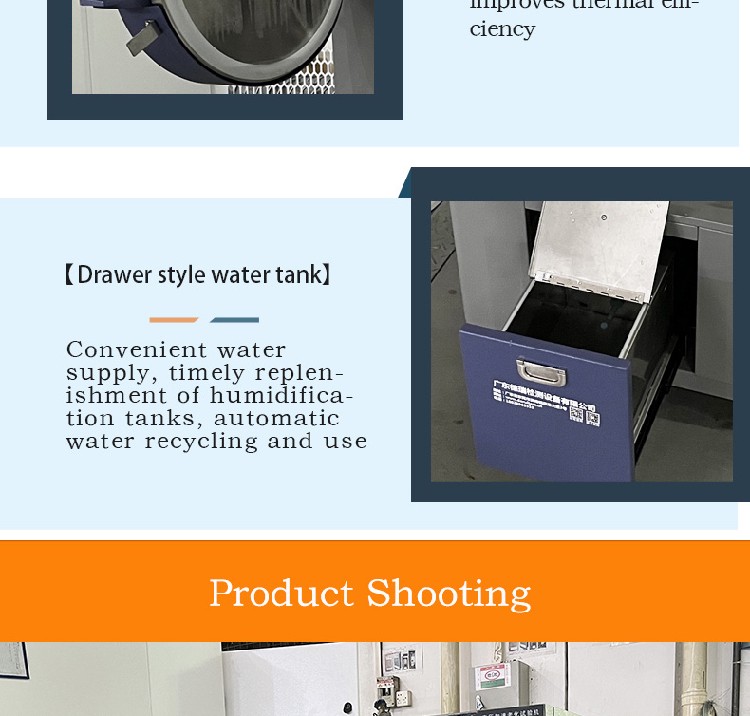
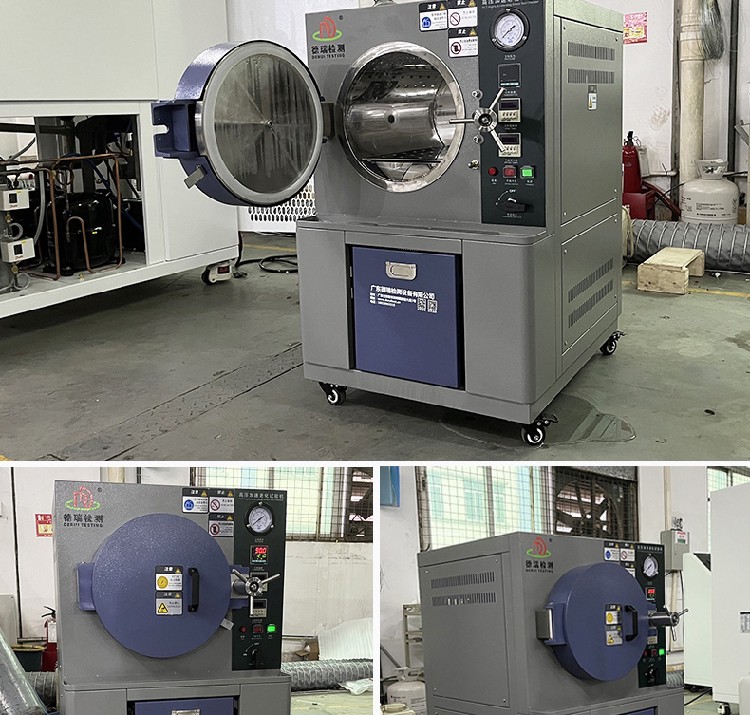
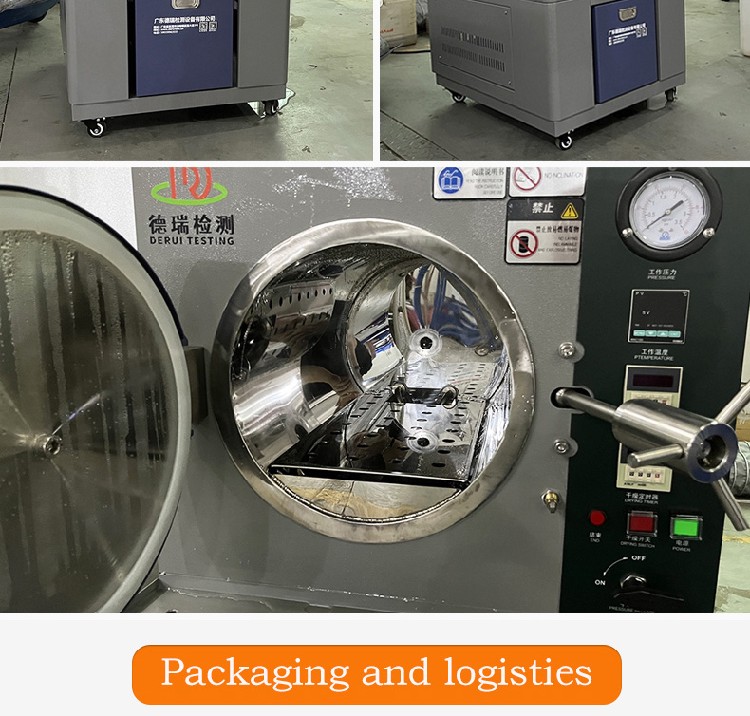
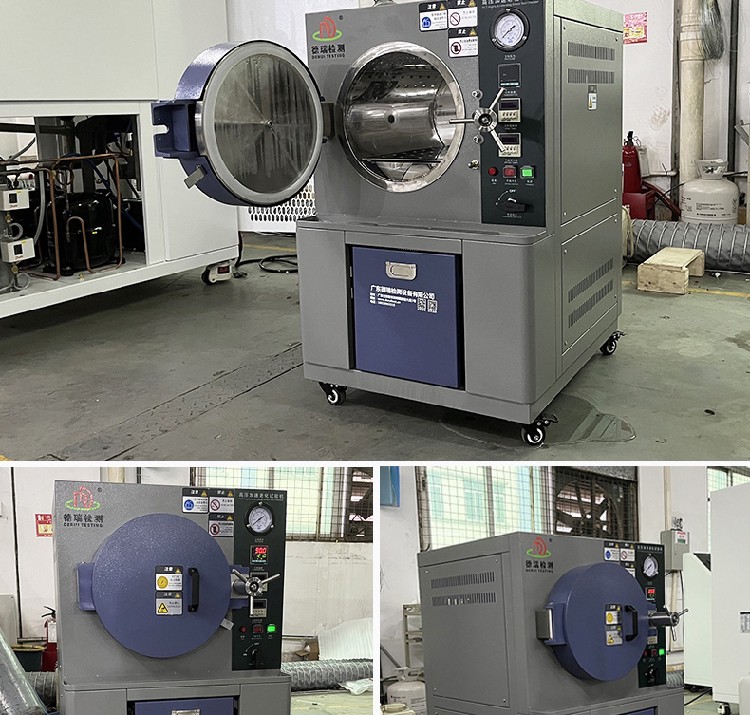
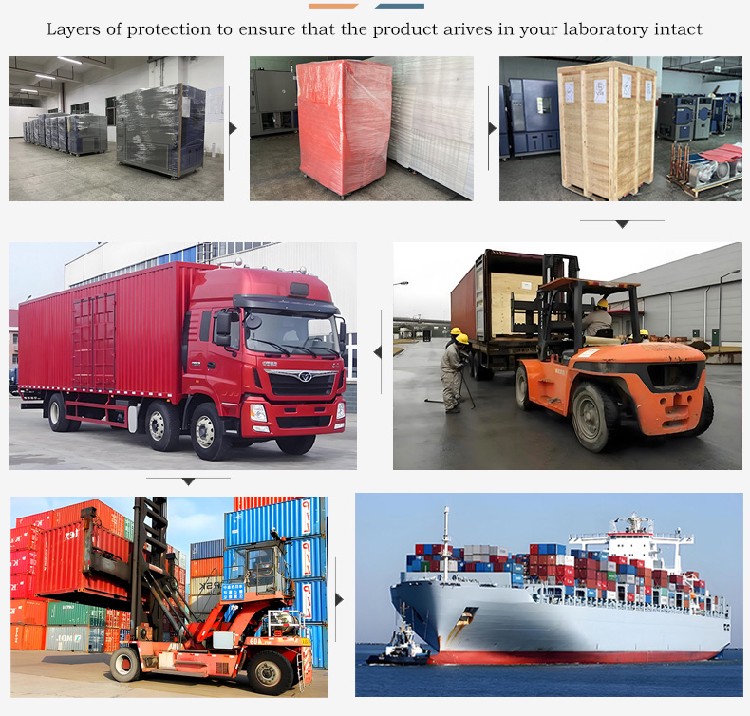
An Electronic Component HAST (Highly Accelerated Stress Test) High-Pressure Accelerated Aging Test Chamber is specifically designed to simulate harsh environmental conditions that electronic components (such as semiconductors, integrated circuits, printed circuit boards, and other sensitive devices) may encounter during their lifecycle. This chamber accelerates the aging process of electronic components by exposing them to high temperature, high humidity, and high pressure in a controlled environment. The goal is to identify potential weaknesses, predict the lifespan of components, and ensure reliability under extreme conditions.
Key Features of an Electronic Component HAST High-Pressure Accelerated Aging Test Chamber:
- High-Temperature Control:Temperature Range: Typically from +85°C to +200°C, but some models can reach up to 250°C or higher, depending on the chamber design. These elevated temperatures accelerate the rate of degradation in electronic components, mimicking long-term use in harsh conditions.Temperature Uniformity: A high degree of temperature uniformity within the chamber ensures that all components are exposed to the same stress conditions for consistent and reliable results.
- High-Humidity Control:Humidity Range: Typically between 85% to 98% relative humidity (RH). The high humidity helps accelerate the corrosion process in metals, oxidation of semiconductors, and degradation of other materials within the electronic components.Condensation Simulation: The combination of high temperature and high humidity can lead to condensation inside components, especially in the case of PCB assemblies, which can mimic real-world scenarios of short-circuiting or degradation.
- High-Pressure Control:Pressure Range: Usually 2-3 bars (200-300 kPa), but some chambers can achieve pressures higher than 3 bars for more extreme conditions. The elevated pressure simulates deep-sea environments, high-altitude conditions, or sealed enclosures (e.g., aerospace applications).Pressure Cycling: Some chambers can simulate pressure cycles, which are important for testing components that need to withstand rapid changes in atmospheric pressure, such as those used in aviation or space exploration.
- Accelerated Aging Process:Test Duration: The aging process can be significantly accelerated due to the combined effect of high temperature, humidity, and pressure. For instance, a component that would normally take years to fail under normal conditions might fail within days or weeks under these stress conditions.Testing Time Compression: Components can undergo months or even years of stress in just a few days to weeks. This accelerated aging process is essential for manufacturers to ensure that electronic components can reliably perform for their expected lifespan.
- Real-Time Monitoring and Control:Touchscreen Interface: Modern HAST chambers for electronic components typically have a touchscreen interface that allows users to set and monitor the temperature, humidity, and pressure in real-time.Programmable Profiles: Users can create customized test profiles with specific temperature, humidity, and pressure ramp rates, hold times, and cycling patterns to replicate different real-world scenarios.Data Logging: Built-in sensors and data loggers continuously track and record critical parameters during the test. This data can be analyzed to assess the performance and reliability of the tested components.
- Sample Loading and Handling:Sample Racks: The chamber is equipped with racks or trays designed to hold multiple electronic components or assemblies during the test. The components are usually arranged to ensure uniform exposure to the testing environment.Accessibility: Some models allow for easy sample loading and unloading, while maintaining a sealed environment. This is especially important for high-volume testing.
- Safety Features:Pressure Relief Valve: To prevent accidents, the chamber typically has built-in safety mechanisms such as pressure relief valves that activate in case of over-pressurization.Over-Temperature and Over-Pressure Alarms: Built-in alarms will alert operators if the temperature or pressure exceeds preset safety limits.Automatic Shutdown: In the event of a malfunction, the system may automatically shut down to prevent further damage to the equipment or samples.
- Versatile Test Applications:Component Stress Testing: Components such as semiconductors, microchips, capacitors, resistors, and PCBs are all subjected to stress to accelerate their potential failure modes (e.g., oxidation, corrosion, or material fatigue).Component Aging: The chamber helps manufacturers assess how their components will age under extreme environmental conditions, providing insights into the longevity and reliability of the products.
Applications of the Electronic Component HAST High-Pressure Accelerated Aging Test Chamber:
- Semiconductor Testing:ICs (Integrated Circuits): Accelerated aging tests are performed on integrated circuits to predict their failure rates and improve design reliability. High humidity and temperature can cause electromigration, bias temperature instability, and moisture absorption in semiconductors.Semiconductor Packages: The chamber can test the reliability of semiconductor packages, ensuring that the encapsulation and bonding materials hold up under extreme conditions.Chip-on-Board (COB) Assemblies: These assemblies are tested to ensure that the chip and the surrounding components will remain operational even under prolonged exposure to extreme heat and humidity.
- Printed Circuit Board (PCB) Testing:Solder Joint Integrity: The high-temperature and high-humidity conditions simulate long-term exposure to the elements and can cause corrosion of solder joints, which is a common failure point for PCBs.Component Adhesive Testing: The effects of heat and humidity on the adhesives used to bond components to PCBs are tested to ensure the integrity of the bond throughout the product’s lifespan.
- Electronics for Aerospace and:Reliability for Extreme Conditions: Aerospace and electronics often need to withstand extreme pressure (such as high-altitude flight or deep-sea operation), temperature fluctuations, and high humidity. HAST chambers simulate these conditions to ensure that mission-critical components can perform reliably.High-Pressure Environments: Components such as sensors, actuators, and avionics are tested for durability in high-pressure environments, like those encountered in spacecraft, submarines, or high-altitude aircraft.
- Consumer Electronics:Smartphones, Tablets, and Laptops: Consumer electronics manufacturers use HAST chambers to test their products’ reliability over long periods of use, ensuring that devices will continue to function under varied environmental conditions.Battery Testing: Batteries for mobile devices, laptops, and electric vehicles can be tested for their performance under high-temperature and high-humidity conditions, which can affect battery life and capacity.
- Automotive Electronics:Automotive Sensors and Control Units: Automotive components, such as ECUs (Electronic Control Units), sensors, actuators, and connectors, are tested to ensure they remain reliable and functional under varying temperature, pressure, and humidity conditions encountered on the road.Corrosion Resistance: The high humidity and temperature conditions in the HAST chamber simulate conditions that could lead to corrosion, particularly in the electronic components exposed to rain, humidity, or road salt.
- Failure Analysis and Quality Assurance:Defect Detection: The HAST chamber is also used for failure analysis in electronic components. By accelerating environmental stress, it helps engineers identify manufacturing defects, weaknesses in design, or issues related to the choice of materials.Validation of Reliability: Manufacturers can validate the longevity and robustness of components and assemblies, ensuring that they meet quality standards and regulatory requirements.
Advantages of Using an Electronic Component HAST High-Pressure Accelerated Aging Test Chamber:
- Time Efficiency: Accelerates long-term testing, enabling rapid identification of potential failures and performance issues.
- Improved Reliability: By simulating the worst-case conditions, it helps identify vulnerabilities in components and materials, allowing for design improvements.
- Cost Savings: Identifying reliability issues early in the design phase helps prevent expensive product recalls or performance failures in the field.
- Comprehensive Testing: Simulates a combination of high-temperature, high-humidity, and high-pressure conditions, providing a holistic assessment of component reliability in extreme environments.
If you need further information on particular models, specifications, or specific test conditions for certain types of electronic components, feel free to let me know!